The OSRAM PL-530 is one of the most unique solid state laser modules we have worked with. The PL-530 is an Optically Pumped Semiconductor Laser capable of outputting a maximum of 100mW of 530nm laser light. OPSL lasers are similar to DPSS lasers, using additional optical components to convert the wavelength generated by the laser diode into a different desired wavelength. OPSL lasers use a semiconductor rather than a crystal to modify the frequency and wavelength. Making this unit more unique is its incredibly small form factor. It weighs only a few grams and is roughly 14mm by 7mm. Contained within the small metal casing is the laser diode, OPSL semiconductor components, optics, and a PTC heater. OPSL lasers like the Coherent Sapphire contain the same general components as the PL-530, but this unit drastically scales down and miniaturizes everything to allow for a very small form factor. These units can be found on eBay, sometimes with the driver included but are often sold on their own. They are relatively inexpensive, and significantly cheaper than traditional OPSL lasers.
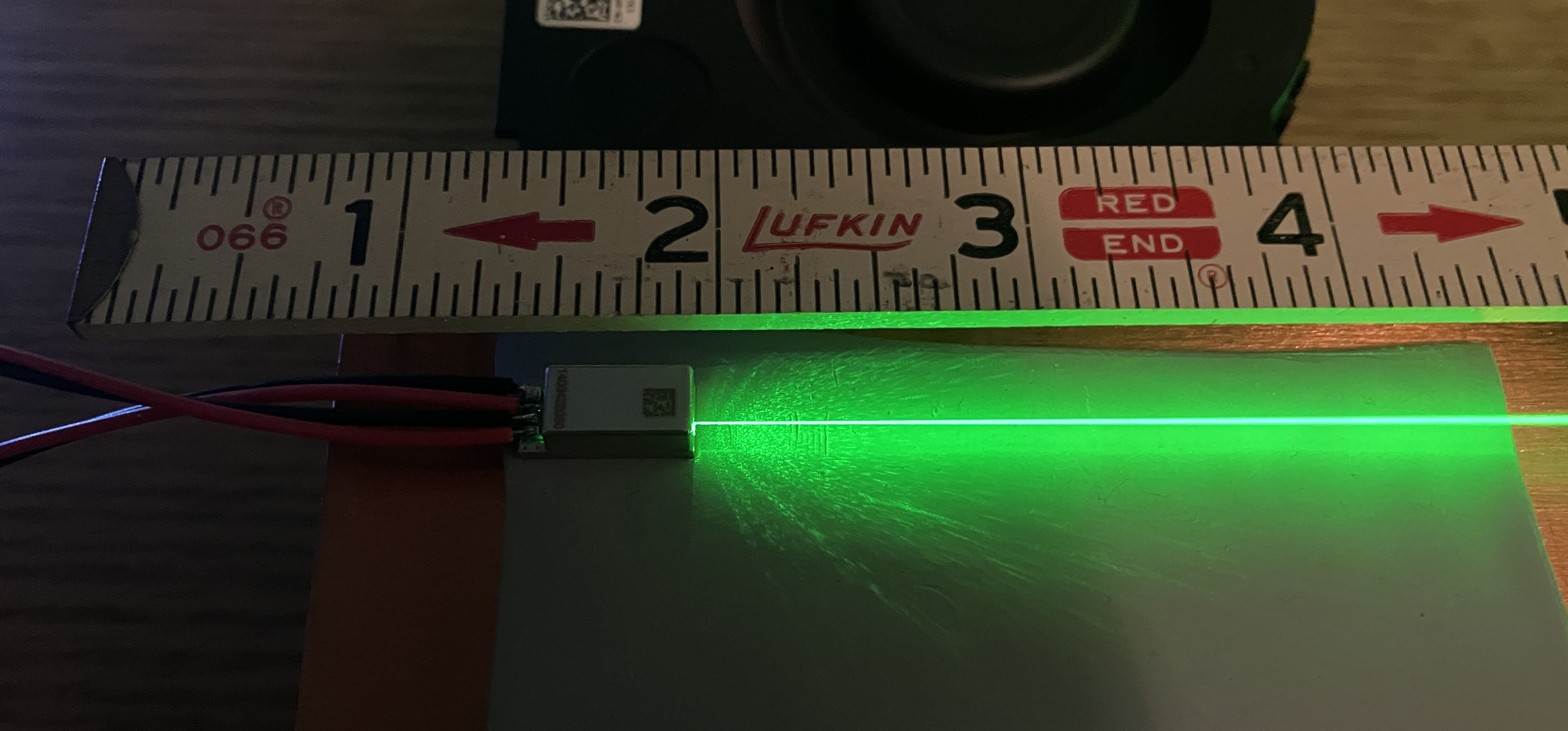
Please note that the image below is not originally ours, and has been modified slightly. It shows the inside of the PL-530, with the top cover removed. This is incredibly hard to do without damaging the unit so we opted to use this image instead of mutilating our PL-530.
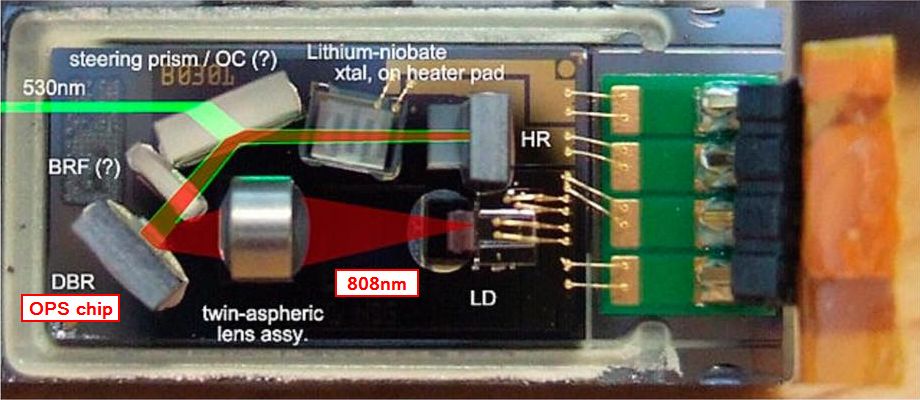
Laser output starts with an 808nm pump diode, it then passes through a twin-aspheric lens assembly. Next is the OPS semiconductor chip (thin silicon wafer), this chip simultaneously works as a gain medium and a cavity mirror. The unique composition of this semiconductor determines the output wavelength, see Coherent's documentation for more details. Light then passes through a birefringent filter (BRF) and then to the output coupler, however it does not yet exit. It reflects off and through a Lithium niobate frequency-doubling crystal, which is mounted on the PTC heater. Light bounces off of a high reflector (HR), back through the frequency-doubling crystal, and out through the output coupler. As the frequency is doubled, the wavelength is divided in half, resulting in the final output wavelength of 530nm. This final process including the frequency-doubling crystal results in second-harmonic generation (SHG), and is a similarity shared with traditional DPSS lasers. In fact, OPSL and DPSS lasers follow a similar process to achieve essentially the same end result, they just use different components. The semiconductor OPS chip allows OPSL laser systems to be more versatile and efficient when compared to traditional DPSS systems. The unique advantage of the OPS chip is the ability for its structure to be modified during manufacturing, which essentially determines the output wavelength (within range), and therefore can be better tailored for a specific industry or use case. The non-linear crystals used in DPSS lasers have set properties and do not allow for this high level of flexibility. Additionally, the OPSL chip is much more efficient at handling higher output power levels from the pump diode. While DPSS systems can achieve high power levels, they are more susceptible to thermal damage and saturation of the crystals. OPSL technology is more efficient at heat dissipation due to the design of the thin semiconductor wafer and can easily reach power levels above 10W.
The PL-530 has 4 connections, see the pinout below. Two connections are for the laser diode, and the additional two connections are for the PTC heater. The PL-530 is designed to be used with a special PCB connector but we opted to solder some thin-gauge wire directly to the contacts instead of attempting to source the uncommon connector. To ensure stability and reliable operation, this laser module should be bonded thermally to a heatsink and TEC for temperature regulation.
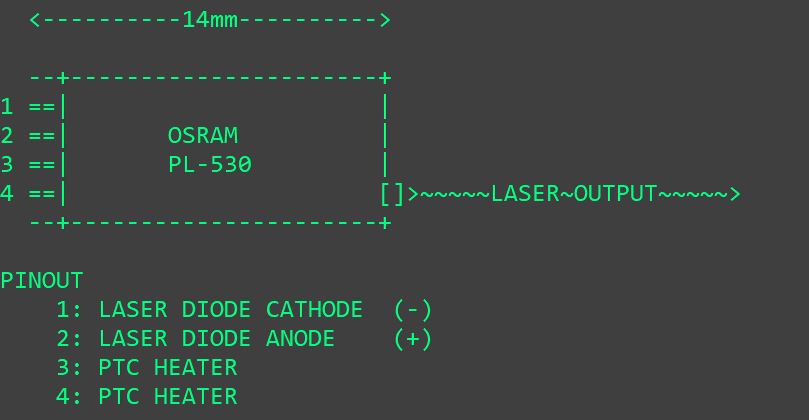
Driving this unit ended up being less complicated than we initially thought. We are very grateful to Zenodilodon who provided useful insight and also sent us his custom PTC heater driver and diode driver boards that ended up working exceptionally well with this unit. Driving the pump diode is relatively straightforward as with any normal laser diode. The datasheet from OSRAM specifies an operating voltage of 1.8v-2.2v and a maximum current of around 450mA. We tend to be conservative with our equipment so we set the ZenDrive (laser diode driver) current limit to around 325mA, which still produces plenty of bright output.
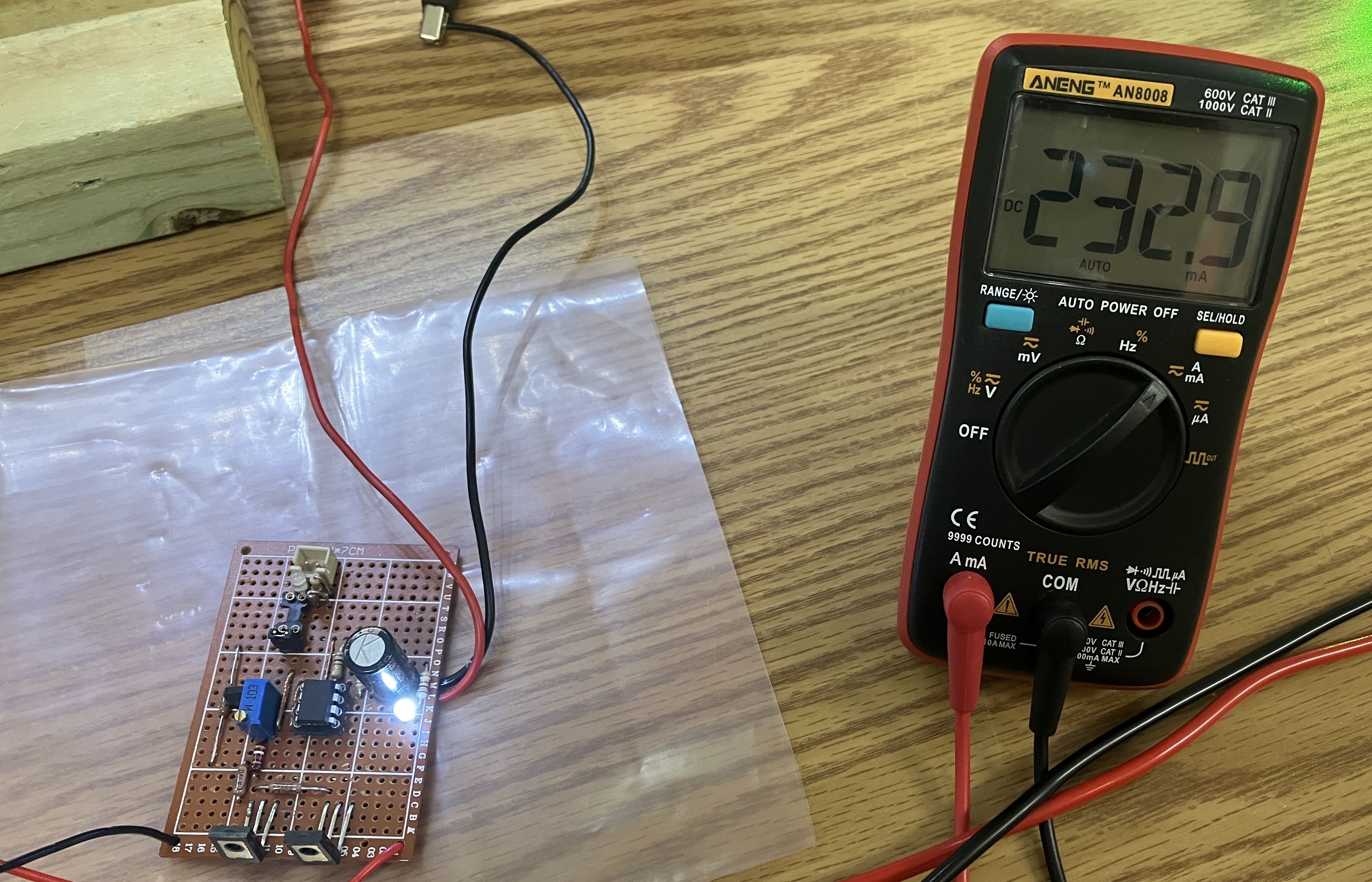
The PTC heater is even simpler to operate, it just needs a constant voltage of around 1.5v-2v. We used the ZenPTC (PTC heater driver) which allows for a bit more granular control over the PTC heater and provides useful feedback in the form of LEDs. It takes a bit of time to get the PTC voltage dialed in just right. Laser output will drastically change as the PTC heater falls in and out of range. Don't become concerned if the beam fades in and out or is very dim, more likely than not, the PTC heater voltage just needs to be adjusted. What worked for us was to set the laser diode current at around 325mA and continually adjust the PTC voltage up and down until the output was bright and stable. Also, regulating the base temperature does help with this as they are designed to be used in conjunction with a TEC for thermal regulation. If you don't have a TEC on hand, a heatsink and fan should be adequate for non-critical applications, just be sure to use a thermal pad or thermal paste between the bottom of the laser module and the surface of the heatsink.
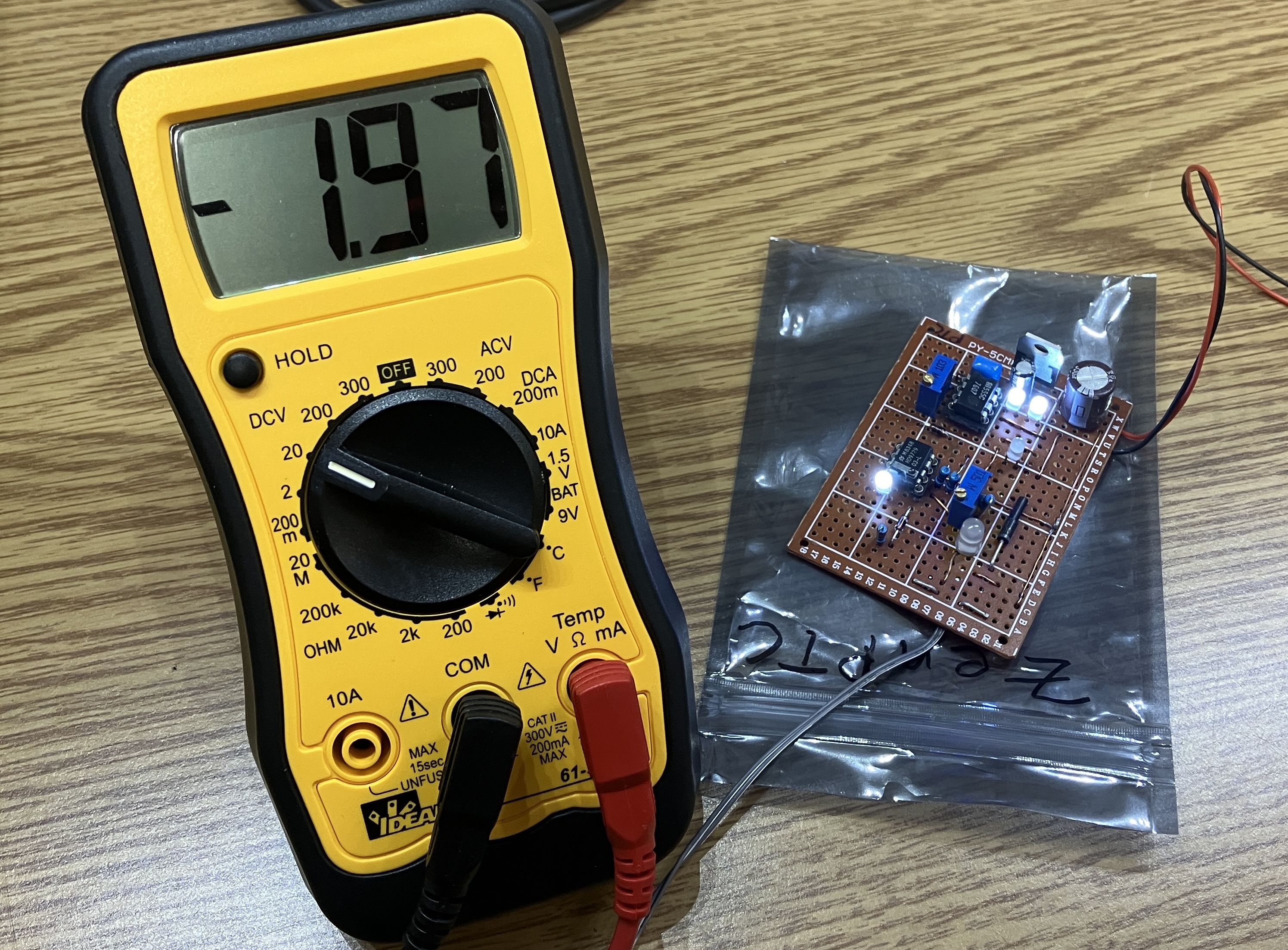
A collimating lens is recommend as the beam diameter increases rapidly once it exits from the tiny output window. Overall, we are very impressed with the output power and beam quality of this unit. OPSL lasers are complicated enough, so it's an engineering marvel to fit all the required components of an OPSL laser into a form factor that fits on the tip of your finger.
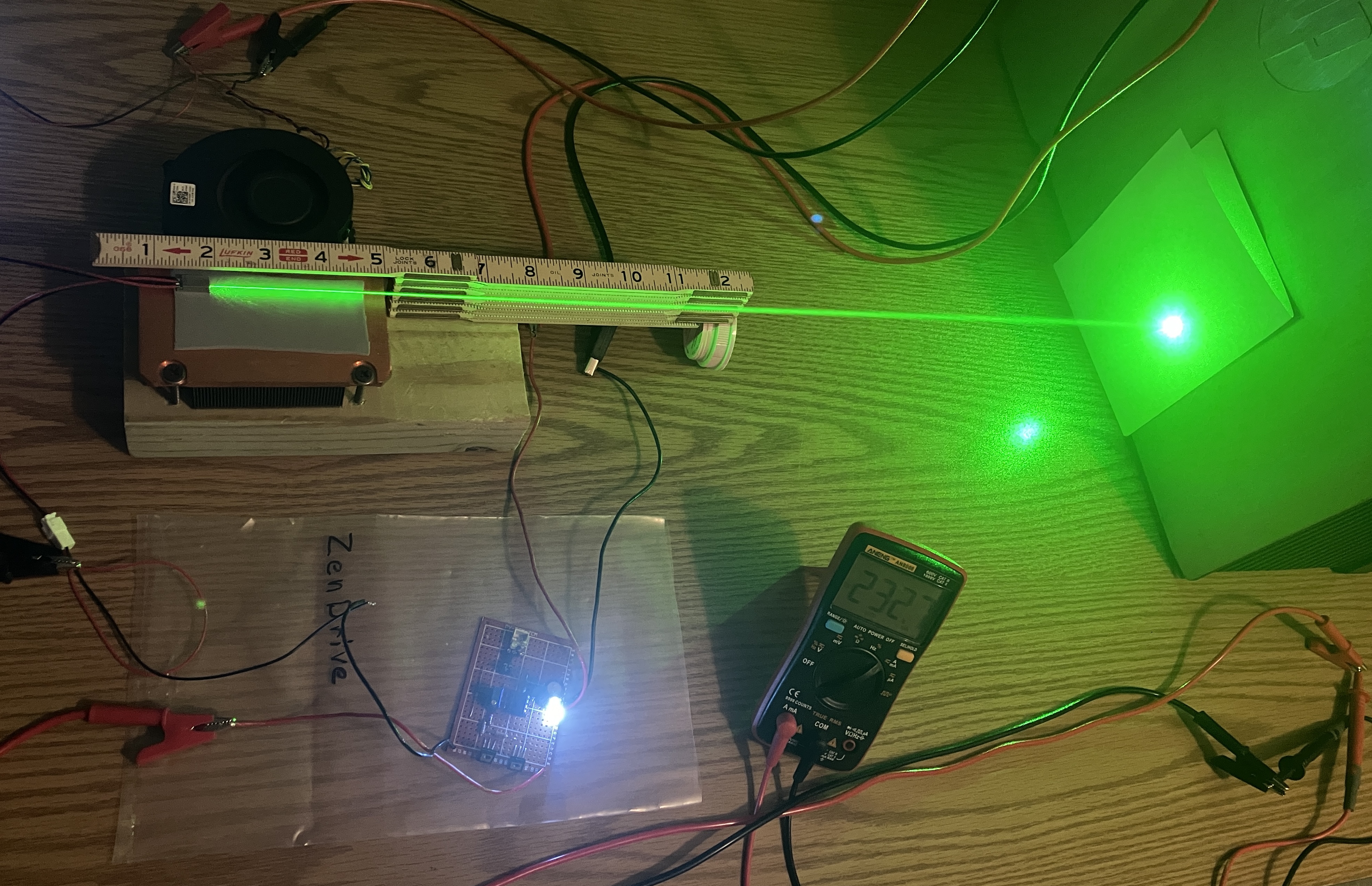
Please visit the links below to learn more about OPSL lasers, their theory of operation, and more about other's experiences with the PL-530.